Natural Colours from Plants
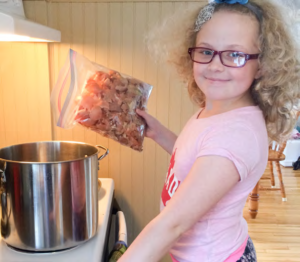
To view the photo-rich magazine version, click here.
Originally appears in the Summer 2017 issue
by Annamarie Hatcher
Experimenting with plants to colour textiles is an exciting experience for all ages. As young artists watch a simmering pot of kitchen waste turn a T-shirt a deep, rich gold they are usually dreaming about their next experiment.
“This is really easy. It was fun to watch colour come from the onion skins. It gets darker and darker the longer it is on the stove. As soon as we started, I wanted to try and do this with beets or carrots next time.” (Claire Beresford, Grade 4)
Integrated curriculum is the aim for many public school systems, and the challenge for teachers is to develop or obtain resources that will support locally-relevant integrated teaching and learning. Life skills such as food preparation and clothing production have provided frameworks for learning opportunities incorporating traditional academic disciplines.[i] Natural dyeing can span the disciplines of chemistry, botany, history, and art. For example, an understanding of chemistry is required to successfully transfer colours from plants to textiles. Students can learn the basics of botany as they experiment with different plants. Curiosity and exploration, the underpinnings of science, underlay the experimentation with potential dyestuffs. History brings in a rich tapestry of stories based on the cultural trade of popular dyestuffs throughout time. Underpinning all of these ‘subjects’ is artistic expression. To achieve certain patterns and effects, students will become artists, learning about colour and light.
There are many paths to follow when developing an integrated unit based on natural dyeing. This article will start you on the journey with basic principles and a hands-on exercise, aimed at grades 4 to 6. This exercise is based on one of the most commonly-used natural dyes, derived from the skins of the common yellow onion. Simmering the skins in water will extract the colour. The deeply-coloured water bath can then be used to impart rich, earthy tones to fibres such as cotton and wool. With simple precautions, this process is safe for young students as is outlined below. If you want to go further, there are many good reference books available. Several are listed at the end of this article.
Fibres to be dyed
Natural dyes are most often used on natural textiles. Animal fibres, such as wool and silk, are protein-based. Plant fibres, such as cotton and linen, are cellulose-based. Dyeing techniques are generally different with these two materials. Because varying molecular structures take up dyes in different ways, interesting patterns often emerge on textiles with a mixed composition. Animal fibres, for example, take up dyes more rapidly and at a higher temperature than their plant-based counterparts. Undyed wool yarn would be a good animal-based material to use in the classroom for a natural dyeing project and white cotton handkerchiefs or T-shirts would be good plant-based materials.
Textiles to be dyed need to be clean so that the dye attaches evenly throughout. Oil, grease, or other coatings can affect the success of your natural dyeing experiment so pre-washing is a good idea. Soak animal-based fibre for 20 minutes in lukewarm water with dishwashing liquid added (1 tsp per 13 litres water). Rinse with clear water which is at the same temperature. If the fibre is plant-based, the soak should be in a bath of lukewarm water with washing soda (1 tsp per 4.5 litres water). Washing soda is available in the laundry detergent aisle of the supermarket.
Experimenting with different plants in the classroom
There is no right or wrong way to produce colours on fibres or textiles. The experience with onion skin dyeing (described below) should be considered a starting point for students to begin their own processes of experimentation. Garden or kitchen waste such as the green tops of carrots, stems and seeds of apples, shells of nuts or the outer leaves of purple cabbage can provide a wealth of colours and the range of materials changes with the seasons. Some plants only yield good results when freshly-picked and some can be dried for later use. Generally, flowers such as dandelion, goldenrod and hollyhocks give the richest colours when used fresh. If these are left to dry, the chromophores degrade and the colours produced are muted. Other dyestuffs such as birch bark and rhubarb roots can be dried for later use. The dyestuff should be dried out of direct sunlight in a well-ventilated area and stored in a paper (not plastic) bag. As a general rule, you should use the same weight of dyestuff as fibre to be dyed. The amount of water does not dilute the dyestuff. Rather, the strength of the dye is a function of the number of dye particles relative to the amount of material to be dyed. The colour particles in the dyestuff are ‘shared’ among the fibres.
Charging the dyebath with colour
If flowers are being used, place them into the dyepot, cover with boiling water and leave to steep overnight. The mixture will cool gradually and should be covered. There may be enough colour in the dyebath after this steeping. If not, simmer on a stovetop for an additional 30 minutes. Bark or nuts will need significantly longer to prepare. They should be soaked in water at room temperature in a covered pot for at least one week. After the week they can be simmered gently for an hour or more. Berries are much more colour-potent so it is a faster process to extract the dye. Crush the berries and add them to dyebath water. Simmer for an hour or so and then turn off the heat. Leave in the covered pot to cool overnight.
Introducing the fibre to the dyebath
After the dyebath has been charged with colour, sieve the solid dyestuff (flowers, bark or berries) out of the liquid. Now you are ready to start dyeing! This may be done using a cool or a hot technique.
Cool dyeing techniques may be more suitable for younger students. Colour development in plant-based fibres often responds well to this technique. In this method, textiles are added to the dyebath and stored for a given period of time, out of direct sunlight. With some dyestuffs such as flowers, an overnight soak will be adequate. For others such as leaves and seeds, several days may be required for adequate colour to develop.
In the hot dyeing method, the textile is placed into a cool dyebath and then the pot is gently heated until the dyebath reaches a simmer. The dyebath is usually simmered for 30 minutes to one hour, removed from the heat and left overnight. The pot can be heated using a conventional stovetop or a slow cooker.
All natural dyes can be divided into those that need a mordant (adjective or fugitive dyes) and those that don’t (substantive dyes). A mordant is an additional substance that facilitates the binding of the dye particles to the fibre (from the Latin word ‘mordere’ meaning ‘to bite’). Substantive dyes are usually those that are rich in tannins such as tree barks and nuts. These tannins work as built-in mordants.[ii]
Mordants
It is likely that these natural dyeing techniques developed as a by-product of daily food and drink preparations. The processes of cooking food and fermenting fruit for alcoholic beverages are similar to those of dyeing fibre. The earliest dyeing experiments probably produced a stain that faded quickly in the light or that washed out when the fiber was wet. Preparing hides for leather may have led to the discovery of tannin-rich tree barks as natural mordants.
Mordants are often metallic compounds of aluminum, iron or copper. Chrome and tin mordants are used by experienced dyers but are too toxic for young novices. Instead, some natural substances such as tree barks and nuts can be used as mordants for adjective dyes. The most effective way to treat fibre with a mordant is before the dyeing process.
Alum powder (aluminum ammonium sulphate) is used in pickling recipes as a preservative and to maintain crispness. It is approved by the U.S. Food and Drug Administration as a food additive, and is safe to use as a mordant with natural dyes in your classroom.
Pre-treating with Alum as a mordant
If a dyestuff needs a mordant, treatment can be done beforehand and then dried and stored for dyeing at a later date. Alternatively, you can use the wet fibers right away.
- Weigh the fibre to be pre-treated.
- Soak the clean fibre
- Prepare a solution of food-grade alum (1g of alum dissolved in 10ml of boiling water). Stir the solution until all alum is dissolved. This solution can be added to the wet textile according to the pre-measured weight. For 100g of fibre you need 8g of alum or 80ml of pre-prepared solution.
- When using alum, it is beneficial to add cream of tartar. This softens the fibre and aids in the absorption of the alum. Add 1½ tsp cream of tartar for 100g of fibre.
- Fill a stainless steel pot with cool water (about 3 to 4L per 100g of fibre). Add alum and cream of tartar solutions and stir to dissolve. Add wet fibre and slowly heat to a low simmer. Simmer gently without agitation for one hour. Turn off the heat and let the fibre cool in the pot, gently stirring occasionally. When cool, remove fibre and rinse gently in cool water.
- After the fibre has been pre-treated with alum and cream of tartar, you can add it to a dyepot or dry it and store for another time.
- Disposal of diluted alum and cream of tartar in standard waste disposal systems is considered safe in most jurisdictions but it would be prudent to check the local situation before disposing.
Safety guidelines
- Use rubber gloves, an apron and protective eyewear. If handling hot pots, use oven mitts. The teacher should closely supervise any activity involving hot pots and liquids.
- Work in a well-ventilated area. If available, the outdoors may be the best laboratory.
- Keep the dyeing materials away from food. Use a dedicated dye pot. Do not eat or drink while handling dyestuffs. Even some natural materials (i.e. rhubarb leaves) can be toxic.
- If you handle powdered dyestuffs, use a mask and eye protection. Even though the alum mordant is safe to be ingested, it will irritate breathing passages and eyes.
Common dyestuffs to try
Students can be encouraged to experiment with many safe dyestuffs collected in the field, forest, garden or kitchen compost. The following have been tested and will produce natural dyes.
- Common yarrow (Achillea millefolium) is a hardy perennial. The plant tops (including flowers) can be used either fresh or dried to produce a soft, yellow colour in fibres which have been pre-treated with alum and cream of tartar mordant.
- Hollyhocks (Alcea rosea) are common garden plants. Dark hollyhock flowers may produce pinks or maroons on animal-based fibres which have been pre-treated with alum and cream of tartar mordant.
- Birch trees (Betula spp.) have been used for dying for centuries. Their leaves can be collected from early to late summer. With animal-based fibres which have been pre-treated with alum and cream of tartar mordant the resulting colour will range from yellow to green. When using birch bark on the other hand, the fibre does not need to be pre-treated because the tannins act as a mordant. The bark should be harvested as shed material on the ground or peeled from cut branches. Avoid removing bark from the main part of the tree to avoid damaging the tree. Treat the bark as described above and use the resulting dyebath to dye wet fibre. Colours from birch bark are usually shades of pink.
- Skin of the common kitchen onion (Allium cepa) will produce a natural dye ranging from yellow, to orange, to rust, to brown. Onion skins are one of the most reliable and versatile dyestuffs. Dyeing with onion skins is a great classroom activity that will introduce young students to the possibilities of working with colours derived from plants.
Where you go from here is up to you and your young scientists/artisans. Experimenting with various dyestuffs to achieve interesting colours and patterns will help your charges to develop an artist’s eye and a scientist’s curiosity. This is a solid base for inquiry-based learning. Planting a dyeing garden may ignite a passion for botany and horticulture, something that often emerges in schoolyard gardening projects. Imagine the engagement that will emerge in a student who follows through on a journey that started with planting a seed and ended with designing and dyeing a unique t-shirt admired by all of his/her classmates. The learning possibilities are almost limitless.
Resources
Casselman, K. D., 1993. Craft of the Dyer: Colour from Plants and Lichens, Dover Publications; 2nd Revised ed. Edition, 272 pp.
Casselman, K.D., 2011. Lichen Dyes: The New Source Book, Dover Publications; 2nd Rev ed. Edition, 96 pp.
Dean, J. & Casselman, K.D., 2010. Wild Color: The Complete Guide to Making and Using Natural Dyes Paperback , Potter Craft, 144 pp.
Vejar, K., 2015. The Modern Natural Dyer: A Comprehensive Guide to Dyeing Silk, Wool, Linen and Cotton at Home, Harry N. Adams, 192 pp.
McLaughlin, C., 2014. A Garden to Dye For: How to Use Plants from the Garden to Create Natural Colors for Fabrics & Fibers, St. Lynn’s Press, 160 pp.
Tanaka, M., 2016. Learning and Teaching Together. UBC Press, Vancouver, 236 pages.
Dean, J., 2010. Wild Color: The Complete Guide to Making and Using Natural Dyes. Watson-Guptill, New York, 144 pages.
Onion Skin Dyeing
Materials
- Large cooking pot and burner/stove
- Alum powder (aluminum ammonium sulphate) and cream of tartar (used for pickles and baking)
- Mild, neutral pH dishwashing liquid
- Oven mitts, safety glasses and rubber gloves
- Tongs for removal of fibres from pot
- Drying rack (clothesline or sweater drying rack)
- Onion skins (many are required so you may want to clean out the bottom of the onion bin at your supermarket or ask friends to save theirs for you). The weight of the onion skin should be about twice the weight of the fibre in order to get a dense, rich colour
- Textile to dye (white fleece or yarn, white T-shirt or handkerchief).
Method
- Clean the textile to be dyed.
- Make the dyebath. Add onion skins to cooking pot and just cover with water. Simmer the onion skins for 30 minutes to one hour. Cool and remove onion skins.
- Treat the fibre to be dyed with a mordant. For dying with onion skins, the fibre should be pre-treated with alum mordant (see instructions above).
- If you are dyeing pre-treated fibre that is still wet, you can add it directly to the dyebath. If the fibre is dry, it has to be wetted so that the dye attaches evenly throughout. The fibre should almost fill the cooled dyebath but still be able to move freely in the liquid.
- Heat slowly and then simmer gently for 30 minutes to one hour. Let the dyebath cool, remove the fibre and rinse with cool water. Let dry.
Annamarie Hatcher teaches Integrative Science at Cape Breton University in Sydney, Nova Scotia. Her courses are imbedded in the geology and ecology of the natural environments of Cape Breton. This article stems from this background blended with her hobby of handspinning wool fibres for locally-sourced textiles. The author would like to thank Rod and Claire Beresford for testing and visually documenting the onion skin dyeing procedure.
Leave a Reply
You must be logged in to post a comment.